Spindle Deep-Dive
Our amazing team member Zeno choose to do a deep-dive for his headstock subsystem design, particularly the spindle. Below he has laid out his entire thought/design process, take a look!

​To begin the design process for the headstock, I set out a number of detailed requirements below to narrow the design space.
​
-
Operating temperature range 0C to 60C
Influences bearing lubrication selection
-
Max operating speed >3000rpm
Influences bearing selection and lubrication
-
Designed continuous operating loads: Axial 100N, Radial 200N
Influences bearing sizing
-
TIR at spindle nose <5 tenths
Adds machining complexity. Measured at <3 tenths
-
Axial unloaded play <5 thousandths
Related to axial preload. Measured at < 1 tenth
-
Radial Deflection 10N preload to 200N load <5 thousandths
Influenced by bearing seals
-
Axial Deflection 10N preload 100N load <5 thousandths
-
Vibration magnitude from low speed to high speed will increase no more than 50% as measured with a phone accelerometer.
-
Expected bearing lifetime and service interval >10,000hr
-
Must be totally rebuildable and require no intermediate maintenance
-
Bearings must be shielded from dust and debris
-
Power loss through the spindle <20% of motor output.
​
After creating these requirements, I proceeded to do a deep dive into bearing design and how they come together to support spindles. I read through the Timken bearing manual, as well as going through the documentation on the SKF website. There is so much interesting information out there! In learning more about bearings and how they function, I came across the field of Tribology, and have started reading Introduction to Tribology by Bharat Bhushan which contains a ton of information some of which I even applied in the bearing selection process! The video series by Robin Renzetti regarding spindle design and rebuild also proved very helpful. With all this information about bearings, and how to situate them to support spindles, I was ready to move onto the next step of actually choosing bearing types and sizes, and their positions. This was the point where I ran into another implicit requirement, cost! Matched angular contact bearings are very expensive so my plans of using a set at both ends of the spindle were infeasible. Next, I planned on using tapered roller bearings, but my requirement of shielding and long service interval didn’t exclude open bearing designs completely but would have made them significantly harder to implement. Since the spindle doesn’t have to operate at particularly high speeds, the lubrication requirements are such that a permanently sealed bearing would suffice. In the end I concluded that using a double row sealed angular contact bearing (SKF 3205A-2RS1TN9/MT33) to support the radial and axial loads at the spindle nose, and a sealed deep grove ball bearing (SKF 6304 2RSJEM) at the outboard side to principally support the radial loads from the belt drive. This design decision was a compromise to minimize the complexity of machining as well as staying in budget.
Next came the analysis piece. SKF has a super helpful tool, SKF Bearing Select which allows you to specify bearings, their center distance, and a load case, and will output all the data out could want including rated life, static and dynamic factors of safety, and even an estimation of frictional losses through the system. The way I set up the CAD enabled me to vary the center-to-center distance of the bearings parametrically and thus easily adjust this critical part of the design.
Report from the SKF analysis tool




Preload & Geometry
Above is a section view of the spindle assembly with the bearings pictured. As you can see, by tightening the nuts, axial pre-load is exerted on the bearings pulling the assembly together enabling the axial play to be minimized.
Assembly and Disassembly Considerations
Since one of my requirements is full disassembly and ability to be rebuilt, I had to consider the fits of the bearings both in the housing as well as on the shaft. Typically, the bearing closer to the spindle nose would be pressed onto the shaft, and I was planning to do this as well. However, had I followed this procedure I would have been unable to remove the bearing for replacement later on. To avoid this constraint, I used an interference fit between the housing and the outer bearing race and used a sliding fit between the inner race and the spindle.
Machining Process
The machining process was long with lots of material removal and tight tolerances to hold. I won’t go into all the details of every part, but a few interesting aspects are as follows.
​
To ensure the nuts I bought would not exert any off axis loads to the rear spindle bearing, I first single pointed a section of thread and then faced the nuts holding them such that the axis of the thread form is perpendicular to the faces of the nuts.
​
The spindle itself took a significant amount of machining time, I removed about 15lbs of material and the part only weighs ~1.5lbs! Thus, I had a good opportunity to take some heavier cuts 0.2” depth, 0.012”/rev @470RPM and see the resulting chip formation and metal removal rate. I also think that the way I structured my operations was pretty clever to ensure that when I flipped the part around to do the second op, I could indicate for both radial and angular misalignment when setting the part back up in the 4 jaw. Judging by the <5 tenths run-out at the spindle nose of the finished assembly, I think this carful planning paid off.
​
The last part I want to highlight is the dust cover at the front of the headstock. This washer like part presented some unique work holding challenges, but I was able to use superglue to fixture and do my final facing op before heating to remove.
Final Assembly & Testing
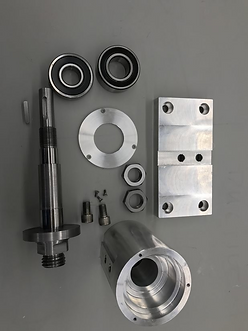
For the final assembly, I was prepared to use a press to seat the bearings in the spindle housing, but after doing some thermal expansion math, I instead opted to heat up the housing with a heat gun and then seat the bearings by hand. It was very satisfying having the bearings unable to fit until the part was warm and then slide in perfectly only to lock in place once the temperatures equilibrated. I also made sure to coat surfaces that would have the potential to gall together with a high-pressure lubricant. For setting axial preload, I ensured that both bearings were fully seated by tightening the nut fully, and then backed off until the spindle rotated freely, but there was no axial play. I measured the play at the spindle nose with my tenths indicator and when pushing and pulling by hand with about 50lbs of force there was no discernable movement.