Mechanical Design ENGR3330:
Mini Wood Lathe Project
Fall 2023

Project Overview
For our project, we aim to design, machine, and assemble a mini wooden pen lathe with 6 adjustable speed settings. We have broken the design into the following subsystems: Structure, Headstock, Transmission, Tool Rest, Tailstock, & Electrical.

Our Project Goals
-
The transmission should employ a belt and pulley system and allow for multiple speed settings.
-
It should have a slow speed for sanding and applying finish, a series of intermediate speeds for turning, and a fast speed for polishing. In the range of 500, 1500, and 3000 RPM respectively.
-
-
The lathe matches the standard parameters of other lathes in its form factor: 10 in turning diameter, ½ HP, 6 in tool rest, 15in center height, 18 in minimum bed, 3.5 in of travel on the tailstock.
-
8TPI #2MT tapers to interface with chucks and mandrels we have in the woodshop.
-
Our lathe should include a custom designed bed & structure instead of modifying an existing wood lathe.
-
The spindle can withstand far past its expected life without significant maintenance.
-
Tool rest and tailstock secure using an eccentric CAM lock mechanism.
-
Machine most, if not all machinable components of our final product.
-
All electrical components need to be safe from dust and not pose a risk for users to interact with.
-
Our final product should be functional enough to turn soft wood with a stretch goal of turning hardwoods, acrylics, and epoxies.
Our Subsystems
Headstock

Tool Rest

Tailstock

Structure

Transmission

Electrical
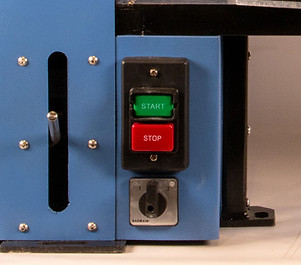
Machining
Since one of our project goals was to machine as many of our own lathe components as possible, a majority of our project took place in the machine shops here at Olin! Here are a few pictures we captured of our team members at work.
Project Takeaways & Future Work
Takeaways
-
You need to consider manufacturing time heavily when designing parts. Even if you are fabricating it yourself, it can be a very large time commitment to make very complex parts. You should simplify where possible and design for manufacturing, not find a way to manufacture your design.
-
Welding yields very bad tolerancing and squareness. Of course, most of us are novice welders, and a more experienced professional could have kept closer to the desired dimensions, but the inherent inconsistency of welding must be accounted for in your design.
-
Having a well-established plan of how the entire system is going to function before going into the specific nitty gritty bits creating models of your designs can be very helpful. If you can flesh out your ideas, you will need to retroactively fix your work much less frequently.
-
Relying on scavenged parts can be risky. We used a salvaged motor from a thrown out washing machine, but it took us weeks to secure one that worked properly preventing us from cementing our designs until late in the process. Sometimes the extra cost of something you can be sure of may be worth it.
Future Work
-
With a more expensive, smaller, and more efficient motor we could cut down the size of our sheet metal and transmission housings
-
Cast iron parts, which are more rigid and easier to mass manufacture.
-
Reducing complexity where possible. Our assembly is close to 180 parts. That could very likely be cut down in future iterations of the project.
-
Incorporation of a pantograph-style guide that moves the cutting tool by copying a template into a cut profile.